Why plastic sliding rollers? Part 2
Bastian Mehr | 9. April 2020
What can be done with a plastic sliding roller?
Here we must clearly compare the cost-benefit factor. Basically, a solid plastic roller is a cost-effective component: of course, depending on the material and the production process behind it. But the plastic roller has its limits. Here one must assess whether the application is suitable.
With a plastic roller, we work with wear throughout the service life X. Here it must be clear to us that after a certain period of time the roller has reached a certain amount of clearance. This limits our service life and must be taken into account at the end.
Usually we move in the range of speeds up to 1m/s and loads up to 0.5MPa. In this range we can work well with plastic rollers. Many rollers are made of UHMPE and used with water lubrication. That works well, too. However, if we wish to dispense with lubrication completely, other materials have to compensate with their properties. We are therefore talking about dry operation without any lubrication. Also the slideway does not have to be lubricated.
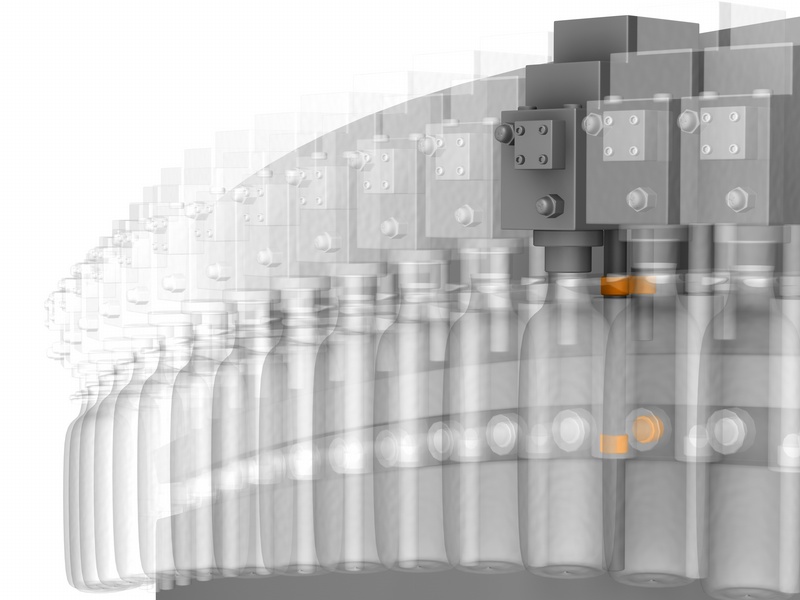
But what often leads to problems is the extreme increase in load when dipping into the sliding. Here the load is briefly increased by a factor of x times. This must be taken into account. In the same way, intermittent operation has a positive effect on the service life.
But what is very important is that the roller really rolls and doesn’t skid. If the load on the roller is too low, the service life may also be significantly reduced. When the rollers skid, they may flatten, which makes neat rolling impossible.
If the loads are too high or the p x v value is too high, wear on the outer diameter can also occur. Also the application temperature must not be neglected. It has a strong influence on the expected wear.
The service life is not easily calculable.
Even though we perform thousands of tests in our laboratory under the most diverse conditions, sliding applications are very difficult to calculate. Every slideway is different. Each position of the roller on the track behaves differently. Starting with the radius at d2 up to the width of the roller. Everything has an impact.
The material of the slideway and its surface has a great influence on its durability. Due to their properties, some materials are more suitable than others. For this purpose we have a lot of data that we can fall back on. But what has a greater effect on the outer diameter is the surface. If we have a slideway that is simply lasered, the roller will wear on the outer diameter. This must be prevented if possible. Slight wear cannot be prevented; however, it should be as low as possible. The actual wear should take place at d1. The counter partner in the form of the axis is decisive for this. Both the material and, more specifically, the surface have a very large influence on wear and on the service life. Here we can draw on the experience of many tests and support you with the right material pairing.
As a result of innumerable tests and many implemented applications for customers in practical terms, we can usually make a very precise statement. We then confirm this with a practical test in real applications. A practical test is usually unavoidable in order to consider all other influences that cannot be calculated.
What does the series solution look like?
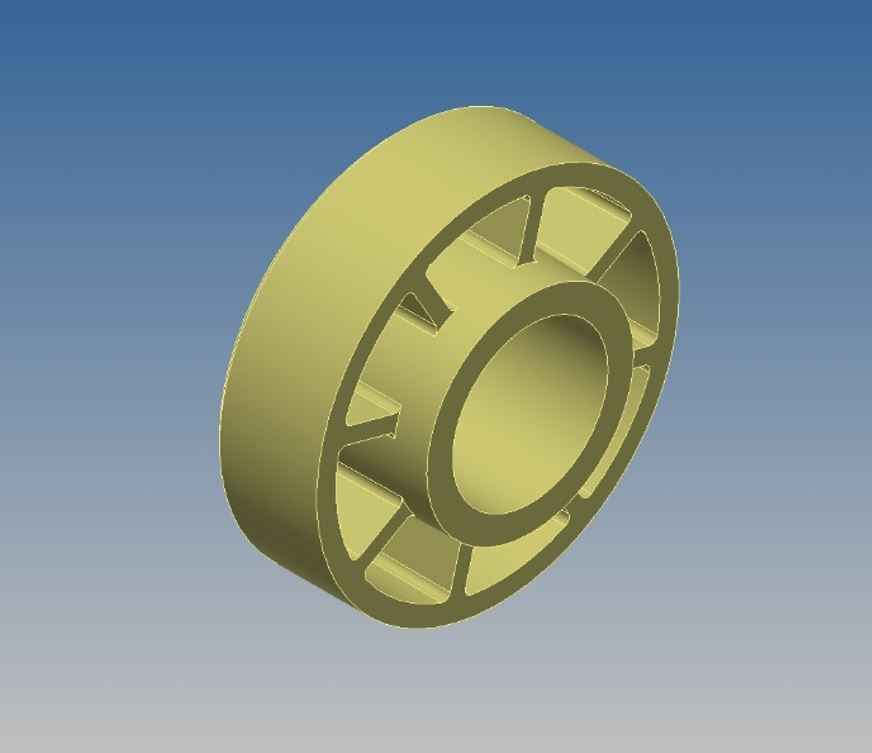
After the successful tests carried out with mechanically manufactured rollers, mass production must now be considered. Here we are dependent on two factors.
- What is the expected volume of production?
- What do geometry and tolerances look like?
In order to make the decision for a volume production solution, it is important to know the expected quantities. Depending on this, it is then checked whether the investment in an injection moulded part pays off or not.
However, the required geometry is just as important. Do we even have a chance to reproduce the roller in injection moulding or are the tolerances much too tight? Another important point is the size or rather the wall thickness of the roller. Here, wall thickness reductions with additional bracing are often necessary for an injection moulded part.
Do you have any questions? We will gladly support you with your design
This is only a brief outline of this complex issue. We would be glad to advise you individually here and support you in your design.