How to optimise every component for injection moulding
Lars Butenschön | 29. January 2021
It is a designer’s worst-case scenario: days and weeks go by to design and manufacture an injection mould. When production finally begins and the first component falls out of the mould, one gets a nasty surprise. The surface of the moulding has dents that not only look unsightly but also impair the function.
Why is this?
The phenomenon is called shrinkage. Hot plastic expands during injection moulding. During cooling, the material shrinks in the mould – the shrink factor is between 0.2 and 2 per cent of the part volume. That is physics and unavoidable.
The problem: the component does not shrink evenly. While external surfaces cool down quickly, the process takes longer in places with lots of material. This causes stresses in the component. They cause parts of the outer surface to cave in and openings to appear. In addition, there is a risk of cavities forming inside – micro-cellular to bubble-shaped cavities that reduce stability. Tolerances are difficult to control for both deformations and cavities.
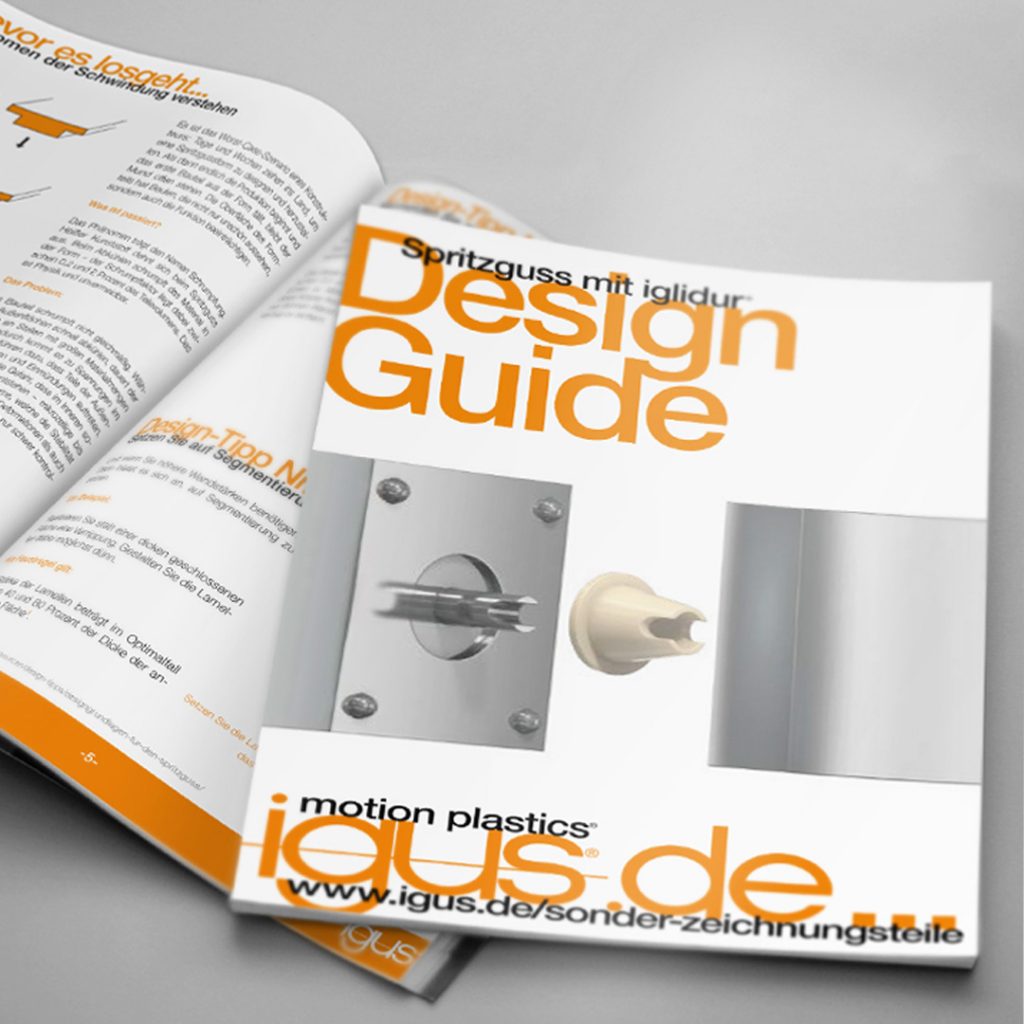
The solution: avoiding wall thicknesses in injection moulding
Keep the phenomenon of shrinkage in mind during the design phase so that effects are not visible. This is achieved by avoiding excessively thick walls and mass accumulations.
The ideal thickness – depending on the material – is between 0.5 and 2 millimetres. If objects in corners lead to accumulations of material, it is advisable to place
these bodies free-standing and secure them against lateral deformation with a thin wall or supports.
But what should be done if the wall thickness cannot be reduced?
Find out in our free Injection Moulding Design Guide, how you can further reduce the wall thickness of your injection-moulded component, and save a lot of money in mould production through other small and large measures.