Crane main power and data supply, proven and alternative systems
Theo Diehl | 9. April 2020
For crane main power and data supply a motor cable drum or – for short travels – a spring tension drum is usually used. Busbar systems for the main power supply are also very common in indoor cranes. As an alternative to the two solutions, an energy chain can be used, which can offer various advantages.
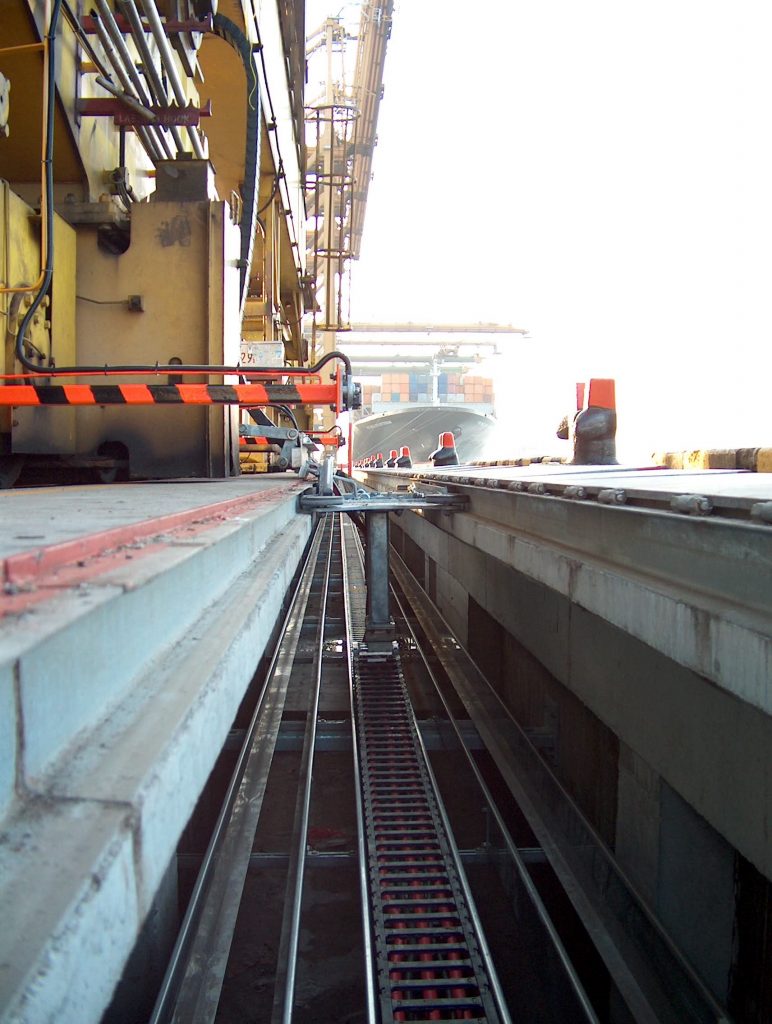
In this article we would like to compare the drum solution with the energy chain solution. The comparison between busbar systems and energy chain is dealt with in the article Indoor Crane Main Power and Data Supply.
System description: motor cable drum
In the drum solution, the cables are guided from the distribution to the cable drum and clamped onto the slip rings at the drum inlet. On the opposite side, the slip ring body is again clamped onto the cable. When the crane moves, the cable is wound or unwound on the drum – usually in a spiral form.
The power, control and data cores must be combined in a trailing cable.
The drum is attached to the crane, the entire weight of the cable, drum and steel construction must be carried by the crane. For long travels (over 200m), several tons of additional weight are loaded onto the crane. At high accelerations and speeds, the additional load has a negative effect on the crane’s energy consumption.
As you can see the whole drum system is more complex than it appears to be. A drive and a control system are also required. The maintenance effort for the slip rings, the control system with drive, brake, and so on is not insignificant.
Max. speeds of up to 300m/min are possible with a motor cable drum.
System description: energy chain with integrated rollers
The energy chain guide trough is installed on the floor, where the cable would be placed in the motor cable drum. Here, there is a greater assembly requirement for the initial installation compared to the drum solution.
A roof is provided over the entire trough system; this serves to protect against foreign bodies, ice and snow.
The energy chain with – individually selectable – cables is mounted in the trough.
With the energy chain solution, no cable clamping is required in front of or behind the moving e-chain. This saves clamping work during assembly and prevents clamping errors.
In addition, the crane is not loaded with extra weight and the energy consumption of the crane is reduced.
As the energy chain has no slip rings, control system or drive, the maintenance effort is lower and the costs for spare parts are reduced.
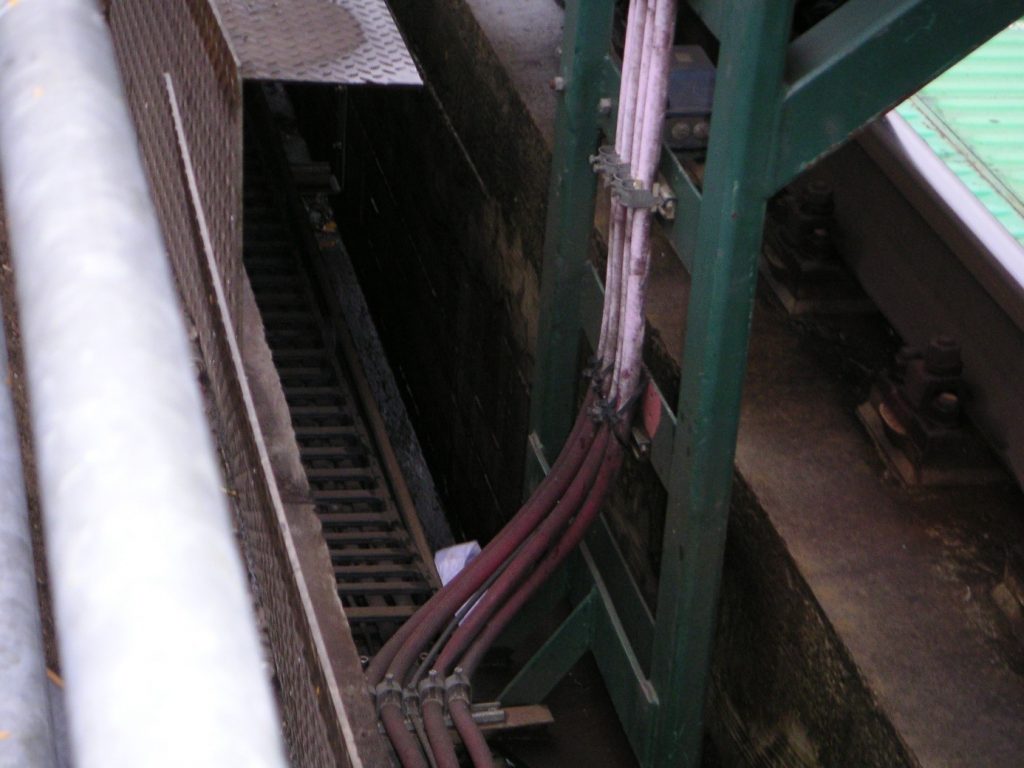
On our website, you will find more examples and solutions for cable guidance in harbour crane applications and our brochure that can be downloaded free of charge.
Do you have questions or an application that you would like to discuss with us? Arrange an appointment for virtual consultation now