ESD energy chains for the ATEX/explosion risk area
Christian Ziegler | 1. April 2020
What does ATEX actually mean? And what is its significance for the selection of my energy chains for the explosion risk area? This is where we give answers to the most important questions.
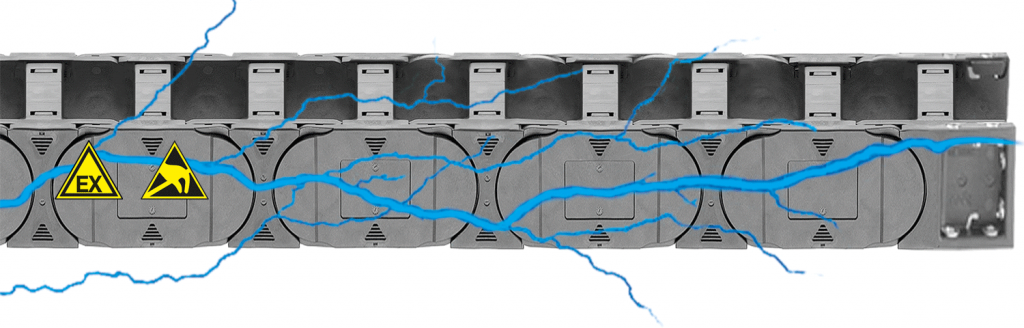
ATEX guidelines
ATEX stands for the French ATmosphères EXplosibles and is used as a synonym for the EU directives governing explosion risk in areas with an explosive atmosphere. There are currently two ATEX directives: the ATEX Equipment Directive 2014/34/EU and the ATEX Workplace Directive 1999/92/EC. The equipment directive formulates requirements for equipment used in explosion risk areas. Explosion risks occur, for instance, in the chemicals industry and in mines, but also in many areas of processing industry: granaries and grain mills, painting systems, woodworking, textile processing, etc.
The equipment directive is used in energy chains assessment. Its definition is clear: a component within the meaning of the ATEX guideline is “any item essential to the safe functioning of equipment and protective systems but with no autonomous function”. Energy chains fit this description.
Requirements of the energy chain
What does it mean specifically for the selection of a suitable energy chain for the explosion risk area? Must the chain comply with ATEX? This question is not that easy to answer. Although an energy chain is a component according to ATEX, the chain itself need not be certified. Why? According to a TÜV Rheinland assessment, energy chains do not fall under 2014/34/EU because they have no autonomous function themselves and must be driven. And because they do not have their own ignition source. Possible electrostatic charge is not by itself a criterion that would place them under the directive.
Conductive plastic energy chains
Because chains do not fall under the directive, chain manufacturers may not declare conformity. The system or machine manufacturer who uses the energy chain, on the other hand, does need to have his system approved by an ATEX inspector. As described above, the possibility of electrostatic charge is not a sufficient ATEX criterion, but there is risk nonetheless: if there is static charge in the energy chain, there may be slight arcing when it discharges. And that can be enough to cause explosive gases or flammable swarf to ignite or explode. This danger of electrical discharge is generally referred to as ESD (electrostatic discharge).
To counteract static charge and this facilitate approval of the overall system, it is helpful to use energy chains of conductive material. In addition to metallic chains, there are also plastic chains of special conductive compounds – this is often called ESD material (short for electrostatic discharge).
Special features of ESD energy chains
Several manufacturers of plastic energy chains offer such ESD designs. During production, a conductive compound is used in the injection moulding tool instead of standard plastic. The shape and appearance of ESD parts is scarcely different from those of standard parts. To ensure that they are not confused with non-ESD parts, igus GmbH produces its ESD energy chains in a different colour than standard ones – slate grey (similar to RAL7015) instead of black.
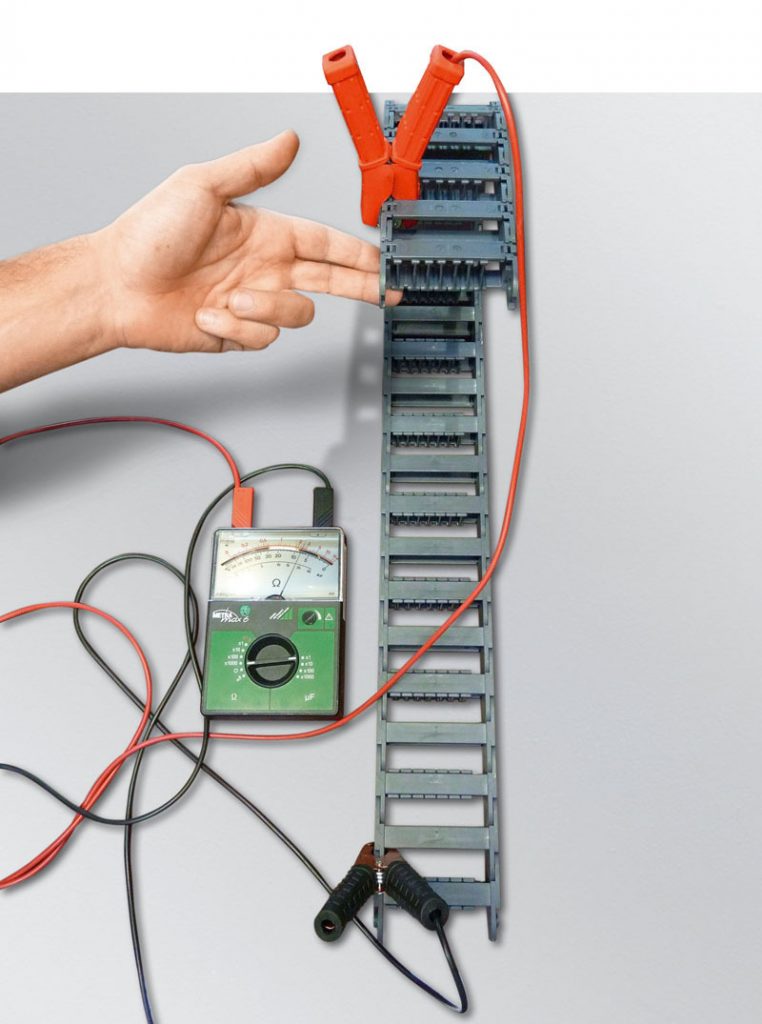
Structural design
In addition to the material, the design of the chain is decisive for continuous, constant discharge. To understand why, let’s look at the example of igus e-chains from the E4.1 modular system: the chain links have a positive-locking connection to one another. The energy chain’s inner links grip the outer links following on both sides. This undercut design ensures constant contact between chain links and therefore millions of cycles of safe discharge.
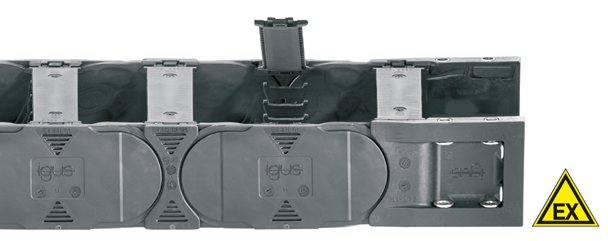
Changed mechanical properties
Despite the same geometry, the mechanical properties of ESD chains are different than standard designs. Values relevant to design, such as maximum fill weight and maximum unsupported length, can deviate from the standard – and tend to be lower. The abrasion behaviour changes when material changes. That is why, for challenging, marginal chain applications, we urge you to consult us: we are happy to advise you – on site or by telephone or digital media (such as MS Teams).
Earthing during installation
In addition to the generally valid energy chain installation instructions, it is important that other installation rules for explosion risk areas be followed: it is especially important that the entire energy chain system be properly earthed. The support base and the connections on both sides must be earthed. For laterally guided gliding energy chains, the guide troughs must also be earthed. And, of course, all installed components must be conductive.
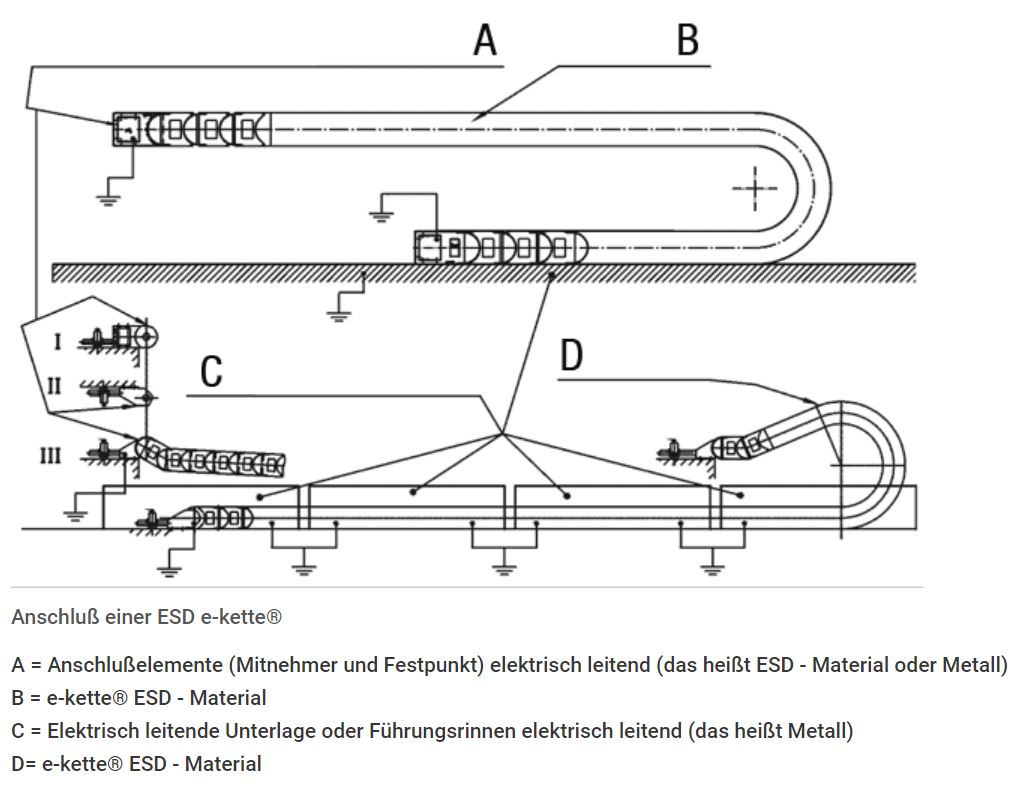
Application examples
There are many energy chain application areas in the explosion risk area. Here are two selected examples: e-chains on a tank wagon and on a deep-drilling rig.
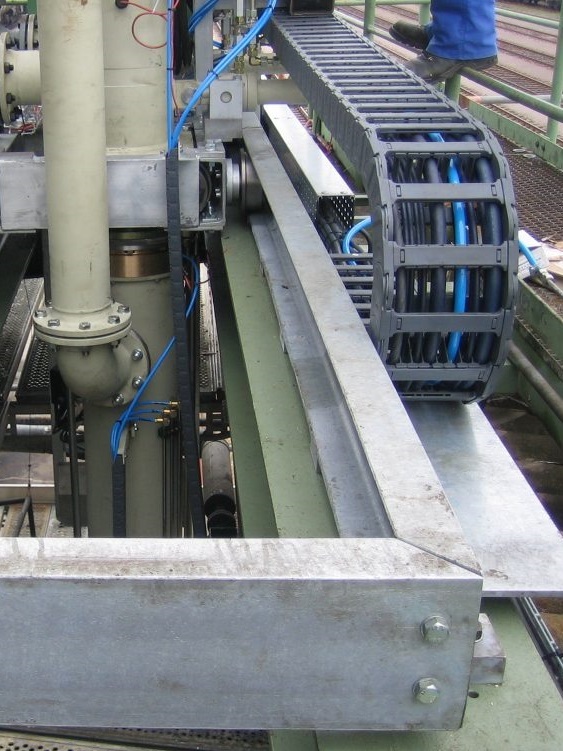
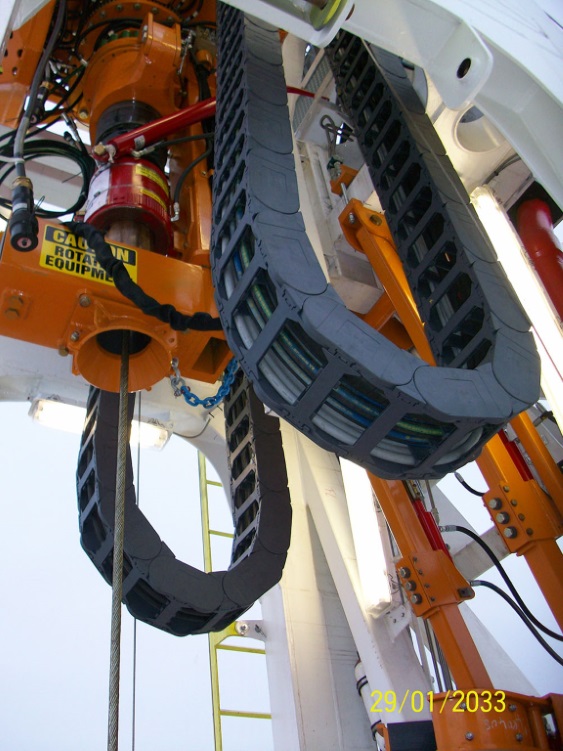
Are you interested in ATEX/ESD? Read the article by my colleague, Lars Butenschön, which provides an in-depth, easily understandable explanation of the issue for the bearing technology area: Plain bearings for the ATEX/explosive risk area – a brief guide