The chainflex genes
7 basic rules for a good cable
Katharina Esch | 25. May 2020
Every new employee at igus® is given intensive training regarding our different company products. Cable training is one elementary component of this. In the process, we pay lots of attention to the structure of our cables, to the so-called “7 reasons”. For us, this special structure is very important. Therefore, we would like to explain the 7 basic rules for a good cable in a chain.
There are many different factors that make for a good cable, used in a chain, which enable the cable to be matched perfectly to its diverse applications. For example, our chainflex cables satisfy the same criteria as standard cables that are fixed in position. Moreover, the chainflex cables have additional virtues for applications in an e-chain, as I will explain in the following.
Normally, I use our CF6 control cable to explain these matters.

1. High tensile strength centre element
Standard cables:
When there are 5 or more cores that make up the structure of a cable, a hollow space is created in the middle, as a result of which the cable becomes unstable and the cores are pressed into the middle. Therefore, this hollow space has to be filled. Plastics are often used for this as the hollow space in standard cables is often only filled with any conveniently available material.
chainflex cables:
Here, a high tensile strength centre element is used to fill the hollow space. At the same time, however, it has another function. The high tensile strength centre element absorbs the forces occurring inside the cable during movement. It consists of a special high tensile strength cord.
Tensile forces mainly occur in the bend radius of a cable. These can be transferred to the centre element. It acts as a “shock absorber” and cushions the movements of the cable. This high tensile strength centre element is therefore important, especially in cases involving highly dynamic movements and a large number of double strokes.
2. Optimised copper strand
Standard cables:
The task of the copper strand is to conduct electricity.
chainflex cables:
The main task of the copper strand in chainflex® cables is also to conduct electricity. Our cables were subjected to long-term tests in order to find the right strand. In the end, this was the only way to find the perfect combination of individual wire diameter, number of wires, optimum pitch length and direction for each copper strand. These parameters ensure that the strands do not break during cable movements.
If the copper wires are too thin, kinks and loops can occur, leading to a short circuit. What exactly happens when kinks and loops occur? Kinks and loops occur when wires that are too thin are stretched and compressed during movement, as a result of which knots are formed. The wires are then broken and can pierce the core insulation coming into contact with wires of the “neighbouring” cores, resulting in short circuits. However, if the copper wires are too thick, the cable is no longer sufficiently flexible during movement in an e-chain and the individual wires break.
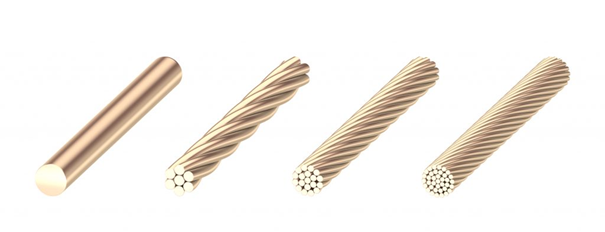
3. Core insulation
Standard cables:
The core insulation ensures that the current is not diverted to the right or left into neighbouring cores.
chainflex cables:
The core insulation of chainflex® cables performs the same task. However, the core insulation of chainflex® cables consists of highly abrasion-resistant material as the cores also have to move within the cable. For the core insulation, we use three different material groups, namely PVC, TPE and XLPE.
4. Stranding
Standard cables:
The cores are only very lightly stranded with a large pitch length. This helps to prevent the cores from becoming loose in the production process when the shield or outer jacket is fitted.
What exactly is pitch length? The pitch length indicates how strongly the cores are stranded together. The shorter the pitch length is, the stronger the cores are stranded together. This means that more material is used and production times are longer.
chainflex cables:
Our stranding method also ensures that the cores remain undamaged in moving applications. We therefore work with a very short pitch length and, in the case of 12 cores or more, with cores wound in bundles. Cores wound in bundles absorb the pull and push forces which occur during movement. These forces occur when the cable moves through a curve (radius). On the inner radius, the cores are compressed and, on the outer radius, they are stretched. We developed the design of cores wound in bundles to ensure that these forces do not place too much strain on the cores, as a core can then continually change its position in the cable. The forces are thus compensated for. This is especially important in order to prevent the so-called corkscrew effect.
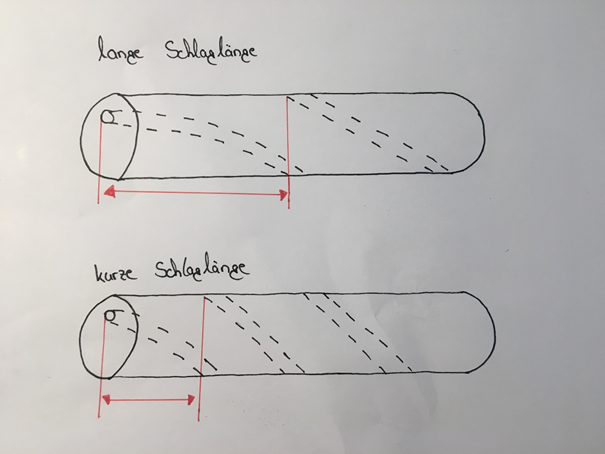
5. Inner jacket
Standard cables:
The inner jacket and/or the filler make the cable round as normal connectors and threaded connections are only designed for round cables.
chainflex cables:
Moreover, the inner jacket of igus® cables serves as the foundation of the shield. The gusset-filled extruded inner jacket guides the stranded structure safely and reliably in a longitudinal direction, in the same way as a train is guided by rails and overhead lines.
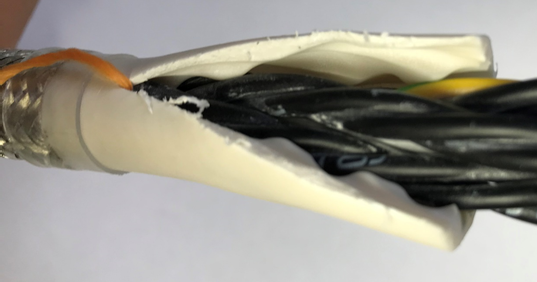
6. Shielding
Standard cables:
The shielding provides EMC protection and protects the cable against interference (link to Jan article)
chainflex cables:
igus® cables have a very flat braid angle. The braided shield adapts itself to the movement of the cable because it can open and close like a pair of scissors during movement. If the braid angle is tight, the shield is unable to adapt itself to movement and can therefore break very quickly. In addition, the shields of chainflex cables have a high coverage of up to 90%, which means very good EMC protection.
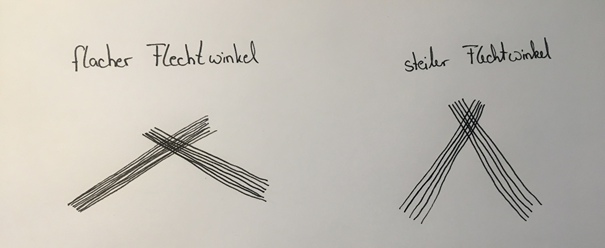
7. Outer jacket
Standard cables for fixed installation
The task of the outer jacket is to protect the cable against ambient conditions such as oil, dust, UV radiation and so on.
chainflex cables:
In the case of chainflex® cables for moving applications, the outer jacket is offered in different materials: PVC, iguPUR, PUR and TPE. Therefore, the right outer jacket material for any environment is available. Irrespective of whether the application requires oil-resistance, UV-resistance or resistance to cold temperatures. In addition, all materials are highly abrasion-resistant and have been extruded under pressure.
Do you have any questions about the 7 basic rules for a cable or do you need further information in this regard? Request a sample or contact us for a personal consultation.