Is the surface in 3D printing too rough for wear-resistant parts?
Due to the layer structure and the production without tools, 3D-printed parts have a higher surface roughness. The higher surface roughness can lead to an initially higher coefficient of friction, as shown below (iglidur I3). After a short period of time, the mating surfaces have “worn out” so that the roughness and coefficient of friction decrease. Therefore, smoothing the surfaces before use is not technically essential.
The run-in behaviour shown so far could only be determined for iglidur 3D printing materials. Standard 3D printing materials behave differently, as they do not have an integrated lubrication. (see PA12 in graph).
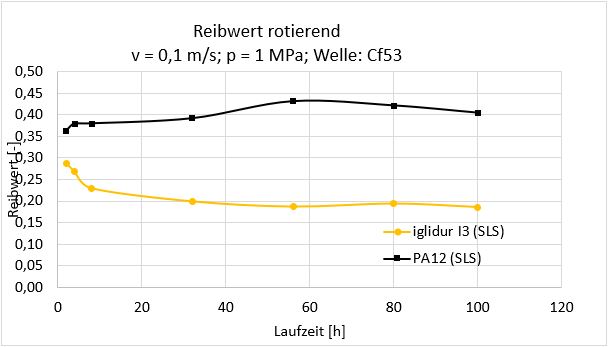
Nevertheless, there are applications in which the components are smoothed after manufacture. Components are smoothed in the following cases:
- Reduce dirt adhesion
- Better look and feel
- Increase impermeability to gas (only with chemical smoothing)
- Better coefficients of friction from the beginning to shorten/reduce the run-in process
How to smooth the surface of 3D printing parts?
There are 3 methods to improve the surface of 3D printed parts:
- Mechanical rework
- Vibratory finishing/ deburring
- Chemical polishing
Mechanical rework:
3D printing parts can be reworked by conventional means for processing plastic components by milling, turning, drilling and reaming. The rework achieves a significantly better surface and precision. The cost of rework is high compared to the other methods.

Vibratory finishing/deburring
In vibratory finishing, the components join ceramic grinding wheels and a coolant in a drum. When this drum is rotated, by the relative motion of the grinding wheels to the components, small amounts of the plastic are released at the component surface, thus smoothing the component.
The process has limitations in terms of component size and component stability, because very delicate components would be damaged in the process and therefore, a minimum wall thickness of 1 mm is recommended.

In order to process several hundred components in one operation depending on the size, this is the most cost-effective method for smoothing 3D printed components.
Further information on vibratory finishing can be found here: https://blog.igus.eu/vibratory-finishing-of-additively-manufactured-plastic-components/
Chemical polishing
Here, the component is briefly exposed to the vapour of a chemical, so as to smooth the surface. In general, a chemical is used here, in which the used plastic is unstable. This makes it possible to smooth the surface in a short exposure time. The costs are higher than with vibratory finishing. However, the surfaces are then also much more strongly smoothed than in vibratory finishing and also somewhat sealed.
Further information on chemical smoothing can be found here: https://blog.igus.eu/chemical-smoothing-of-3d-printed-plastic-components/
