Alternatives to bearings with lubrication groove
Lars Butenschön | 17. September 2021
Lubrication grooves perform an important task in metallic bearings. The lubricant reaches the bearing point between the bearing and the shaft directly through them. The lubricant protects the shaft and bearing against dirt and moisture and ensures low coefficients of friction.

Disadvantages: On the one hand, a bearing with a lubrication groove is quite complex to manufacture, since the groove represents an additional machining step and, depending on the dimensions of the bearing, the inner diameter is difficult to achieve with cutting tools. On the other hand, the permanent supply of lubricants can only be guaranteed by seamless maintenance.
Either the lubricant must be manually replenished regularly using a grease gun or similar, or automatically replenished via an expensive central lubrication unit. Last but not least, the lubricants end up in the environment. The lubrication grooves guide the lubricant through the bearing position to the outside. An aspect that has become increasingly important in recent years. It is no longer “irrelevant” where the lubricants end up.
So it stands to reason to look for alternatives. How could you do without lubrication grooves? And perhaps design the lubrication differently?
Alternative 1: sintered bearings
Sintered bearings approach the problem of lubricant distribution in a similar but slightly different manner than solid bearings with lubrication grooves. Sintered bearings consist of metal grains pressed together and fused under high pressure. After the production process, the cavities remaining between these granules are soaked with lubricating oil. The viscosity is selected in such a way that the lubricant only becomes liquid at a certain temperature (which is only reached during operation) and is released in the bearing position.

Benefits:
- If the bearing position is correctly dimensioned and designed, the bearing is maintenance-free.
- During movement, the lubricant is released and when stationary, it returns.
- In addition, sintered bearings are robust and pressure-resistant.
Disadvantages:
- Due to the manufacturing process, the shaping is limited and restricted to thicker walls.
- Oil is only released when the operating temperature is sufficient. If this is not the case, the sintered metal runs directly and without lubrication on the shaft.
- If the oil cannot be retained in the bearing position, the bearings will dry out and lose their good sliding properties.
Alternative 2: composite bearings
Composite bearings can be made of different metals or plastics. The principle is similar in each case. A thin sliding layer provides good sliding properties and a thicker and tougher outer “bearing layer” absorbs the loads.
Depending on the product, these layers consist of very different materials and result in different areas of application. In the high load range with lower movement speeds, composite bearings made of metal with additional lubrication of sliding layers made of POM or similar plastics, have become established. Alternatively, bearings made of wound, woven glass or carbon fibres with special PTFE sliding layers are used.
The most common composite bearing consists of a steel sleeve wound from sheet metal with a layer of Teflon “rolled” onto its inner surface. “The extremely soft and poorly adhering Teflon is removed by means of a sintered and porous layer of softer metal (e.g. bronze). At approx. 10µm, this PTFE layer is slightly thicker than a human hair (approx. 5µm, i.e. 0.05mm).

Benefits:
- Layer structure offers various possible material combinations.
- Due to the outer support layer, even the softest materials optimised for sliding properties can be used in the inner diameter of the bearing, eliminating the need for lubrication.
Disadvantages:
- If the sensitive sliding layer is damaged, wear rapidly increases and leads to damage
- Minimum wall thickness required
- Limited shaping due to layer structure
Alternative 3: plastic bearings
Plastic bearings offer the advantage that solid lubricants can be mixed directly into the formula. There are therefore no load-bearing layers, no lubrication channels or pores from which liquid or lubricants can escape to the outside. Instead, the entire bearing cross section serves as a sliding and wearing part. Plastic bearings are available in many different designs and their applications range from bearings for hinges to high-tech solutions within coolant pumps in sports cars. Due to the chemical composition and the possibility to fuse and mix different components, the respective plastic mixture can be optimised for certain fields of application. Accordingly, there are plastics that provide good sliding properties and strength, especially under high temperatures, plastics specifically for food contact or for use in chemicals.
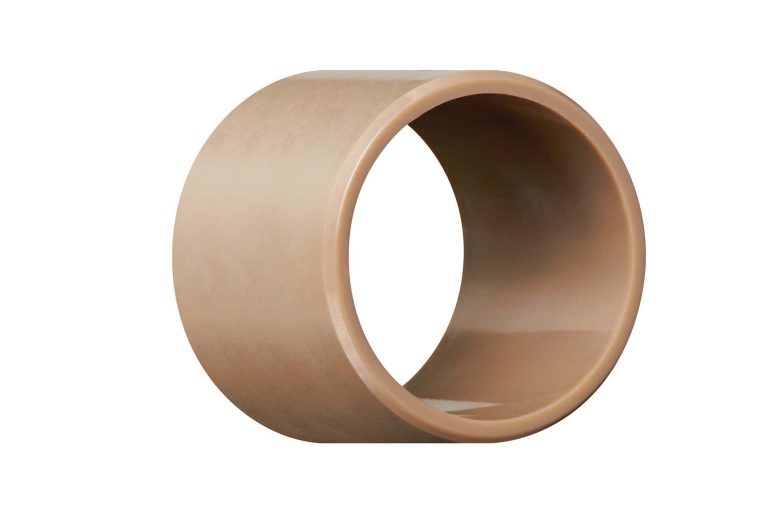
Benefits:
- Great variety for a wide range of applications
- Weight saving compared to metal bearings
- Maintenance-free, without liquid/lubrication
Disadvantages:
- Selection can sometimes be difficult
- Less suitable for very high loads beyond 80-100MPa surface pressure
- Combination of high loads and high speeds difficult due to lower heat dissipation
Are you looking for the best alternative to the bearing with lubrication groove? We would be happy to assist you!
No need to weigh up the various pros and cons. By replacing bearings with lubrication grooves and external lubrication with maintenance-free plain bearings made of plastic, you save costs and increase the reliability and durability of your bearing points. We determine the most suitable bearing solution for you free of charge.