Designing lead screw nuts for 3D printing
Paul Gomer | 24. April 2020
Die zwei häufigsten Gründe für die Fertigung von Antriebs- und Gewindemuttern mittels 3D-Druck Verfahren sind der Bau von funktionalen Prototypen und die Herstellung von komplexen Sondermuttern. In der Produktentwicklung werden mitunter mehrere Modelle konstruiert und getestet – mit dem Rapid Prototyping Verfahren kann die Herstellung von seriennahen Varianten und Anpassungen sehr schnell erfolgen, was einen schnelleren Markteintritt ermöglicht. Die Fertigung von komplexen Sondermuttern ist häufig mit einem großen manuellen Aufwand verbunden, was solche Lösungen schnell sehr teuer macht. 3D-Druck Technologien machen eine Kostenreduktion in diesem Fall möglich – aber auch hierfür wird ein 3D-Modell des gewünschten Gewindes benötigt. Digitale Hilfestellungen können die Konstruktion und Anpassung von individuellen Gewinden erleichtern und beschleunigen.
Einfache Geometrien zylindrisch (Form S) oder mit Flansch (Form F) können schnell und einfach in unserem CAD-Konfigurator für Gewindemuttern individuell konfiguriert und heruntergeladen werden. Die metrischen Gewindegrößen, in Anlehnung an ISO-Trapezgewinde nach DIN 103, der Reihen 1 und 2 sind verfügbar. Fertige Konfigurationen können direkt im Anschluss im Online Druck-Service angefragt oder bestellt werden, was den Konstruktions- und Produktionsprozess von individuellen Gewindemuttern enorm beschleunigt.
Gewindemodelle können am Anfang eines Konstruktionsprozesses bequem konfiguriert und im nativen CAD-Programm Format heruntergeladen werden. Die heruntergeladene Datei kann als Konstruktionsgrundlage für eine komplexe Sondermutter verwendet werden. Bei vollständig konstruierten Modellen, ist auch die schnelle Integration in die bestehende CAD-Datei per Vereinigung von Volumenmodellen möglich. Alternativ wird nachfolgend gezeigt wie die Anpassung im CAD-Modell erfolgen kann (per Funktion: Gewinde/Spirale abhängig vom CAD-Programm).
Wie können Sondergewindemuttern im nativen CAD-Programm fertigungsgerecht angepasst werden
Trapezgewinde müssen für eine funktionsfähige Ausführung konstruktiv für den 3D-Druck vorbereitet werden. Für das Lasersintern kann dies zuverlässig für einen Großteil der Standard Trapezgewindegrößen ab TR8 mittels einkonstruiertem Gewindespiel gewährleistet werden. Eine Kompensation wird nötig, da Innenbohrungen (insbesondere kleine Bohrungen D< 3 mm und tiefe Bohrungen t> 10 mm) sonst grundsätzlich beim Lasersintern, aufgrund von höherem Wärmeeintrag, verengt hergestellt werden. Ursache ist die höhere Wärmespeicherung innerhalb der Bohrung, die zu einem Verschmelzen der Randbereiche führen kann. [Quelle: Generative Fertigung mit Kunststoffen Konzeption und Konstruktion durch selektives Lasersintern: Breuninger, J., 2013]
Hierfür muss das axiale Flankenspiel in Z-Richtung um +0,1 mm und die Durchmesser D1 und D4 mit einem Aufmaß von +0,3 mm am Durchmesser vergrößert werden.
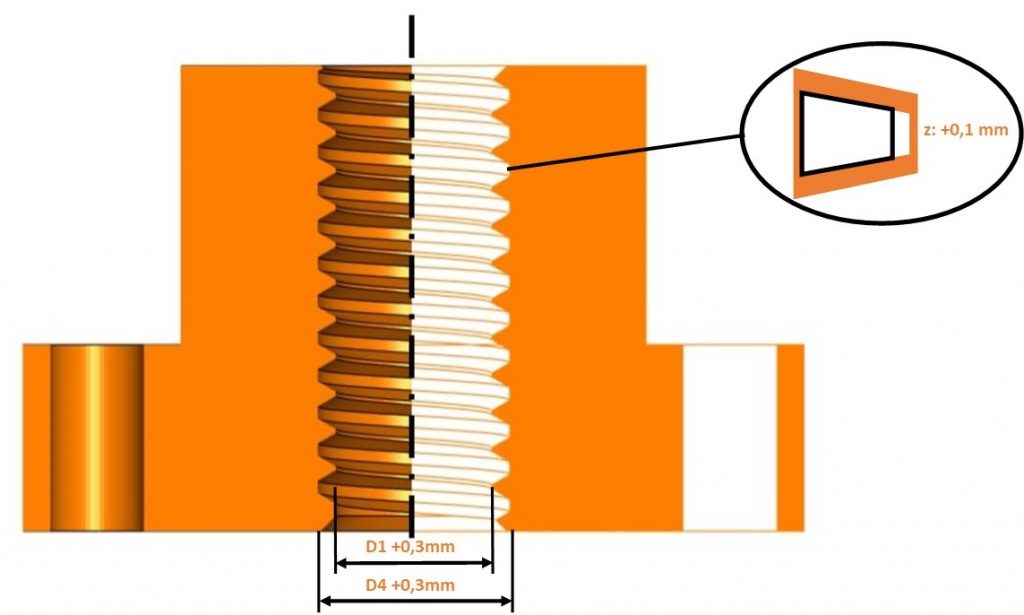
In praktischer Umsetzung im CAD-System heißt das zunächst die Grundlochbohrung D1 um +0,3 mm zu vergrößern. Anschließend muss die 2D-Skizzenkonstruktion des Gewindeprofils nach Tabellenbuch durchgeführt und diese um die beschriebenen Aufmaße angepasst werden. Radial muss +0,15 mm Spiel an der Gewindespitze aufgeschlagen werden (um insgesamt D4 auf +0,3 mm zu vergrößern). Unter Verwendung der Spiral-/ oder Gewindefunktion kann nun unter Auswahl der Drehrichtung und Gewindesteigung das Trapezgewinde ausmodelliert werden, Vgl. Beispielbild TR12x3.
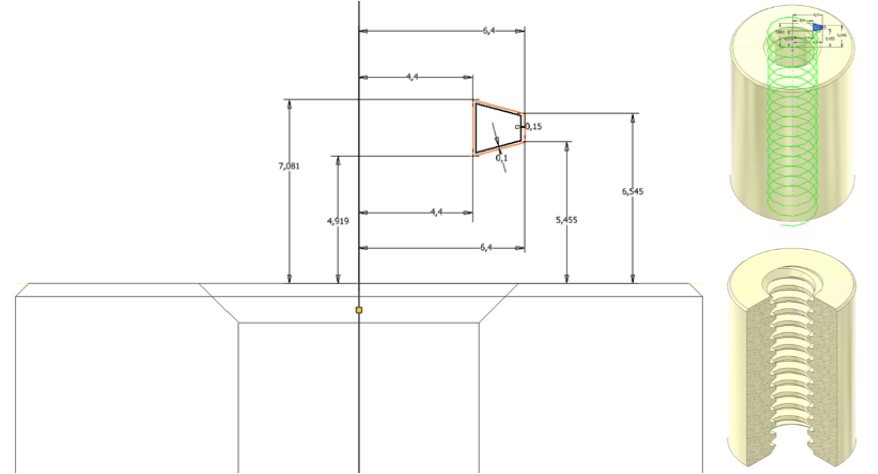
Welche Unterschiede gibt es für die korrekte Erstellung eines Trapezgewindes mit 3D-Druck Filamenten?
Für das filamentbasierte Drucken mittels Strangablegeverfahren (FDM/FFF) müssen i.d.R. neben der konstruktiven Anpassung des Gewindes auch Druckparameter angepasst werden, um ein Klemmen der Mutter auf der Spindel zu verhindern. Geeignete Anpassungen für die Druckparameter können z.B. folgende sein:
- die Reduzierung des Extrusionsfaktors/ Filamentflusses (ca. 5-10%)
- die Verwendung von niedrigeren Schichtstärken: gleich oder kleiner als 0,2 mm
- die Vermeidung von Supportstrukturen, außer ggf. wasserlösliches Stützmaterial
- folgende Druckparameter testen, um eine bessere Genauigkeit in der XY-Ebene zu bekommen:
- Horizontale Ausdehnung: -0,05 bis -0,1 mm
- Alternativ: Außenwände vor Innere Wände aktivieren
Zu empfehlen ist der Probedruck eines kleinen Gewindestücks bevor das ganze Bauteil gefertigt wird. Nötige Anpassungszyklen sind somit stark verkürzt.
Einsatzgebiete für gedruckte Sondergewindemuttern
Die schmiermittelfreie Antriebslösung in der Gewindetechnik reduziert Wartungsarbeiten, senkt dabei die Kosten und erhöht zudem die Lebenszeit der eingesetzten Materialien. Durch den 3D-Druck kommen die bekannten Vorteile, wie der hohen Designfreiheit (Komplexität kosten nicht extra), sowie die schnelle Lieferzeit ab 1-3 Werktagen und die wirtschaftliche Fertigung ab Stückzahl 1 hinzu.
Auch 3D-gedruckte Antriebsmuttern aus iglidur Filamenten und Lasersinter-Materialien finden dabei in vielen Branchen Anwendung:
- Automation/ Prozesstechnik, z.B. Produkthandling in der Verpackungsindustrie
- Maschinenbau/ Sondermaschinenbau, z.B. Sonderantriebsmuttern
- Automobilbranche, z.B. Prototypen für mechanische Schließsysteme
- Roboterindustrie, z.B. Gewinde integriert in Greifmechanik
Anwendungsfall: Wie der 3D-Druck bei der Landstromversorgung von Schiffen in nur 48h helfen konnte
Um die Luft- und Lärmverschmutzung von Hafenstädten zu reduzieren und den Dieselverbrauch im Hafen zu verringern sind vielerorts sogenannte Landstromversorgungen für Container-Terminals und Schiffe für die CO2-Einsparung im Einsatz. Für eine Anwendung für die Landstromversorgung wurden 3 Sondermuttern mit dem Trapezgewinde TR40x14 in nur 48h hergestellt und konnten anschließend im Hafen installiert werden. Da mechanisch bearbeitete Bauteile nicht kurzfristig verfügbar waren und eine hohe Lieferzeit unumgänglich erschien, kam hier die Herstellung der Sondermutter aus dem iglidur I3 Lasersinter-Material im 3D-Druck in Frage. Die dringend benötigten Sondermuttern sind in der Anwendung mit einer max. statischen Last von ca. 1200 kg belastet und konnten wirtschaftlich, ohne kostspielige Nacharbeit, für ca. 300 €/stk. gefertigt werden.
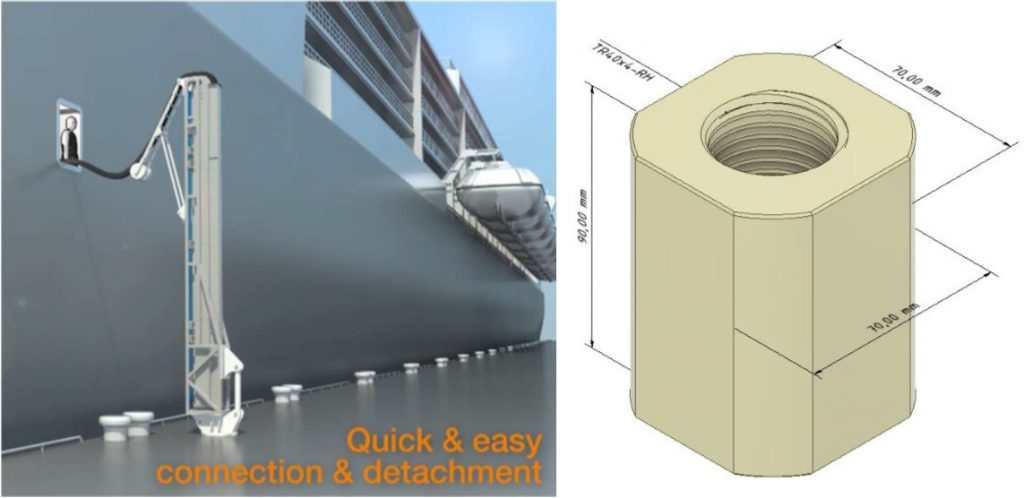
Wie komme ich zu meiner 3D-gedruckten dryspin Sondergewindemutter
Die Fertigung einer Sondermutter kann auf Anfrage auch für dryspin Spindelgeometrien erfolgen.
Welche Vorteile die Verwendung eines verschleißoptimierten dryspin Steilgewindes im Vergleich zu Standard 3D-Druck-Materialien bringt, vermittelt das Ergebnis unseres Labortests für eine Dryspin Spindelmutter DS14x25 bei einem Hub von 370 mm und der Belastungsparameter von 129 N Last bei 290 U/min. Eine geringere Verschleißrate von 5 bis zu 18x besser mittels tribologisch optimierten 3D-Druckmaterialien ist möglich.
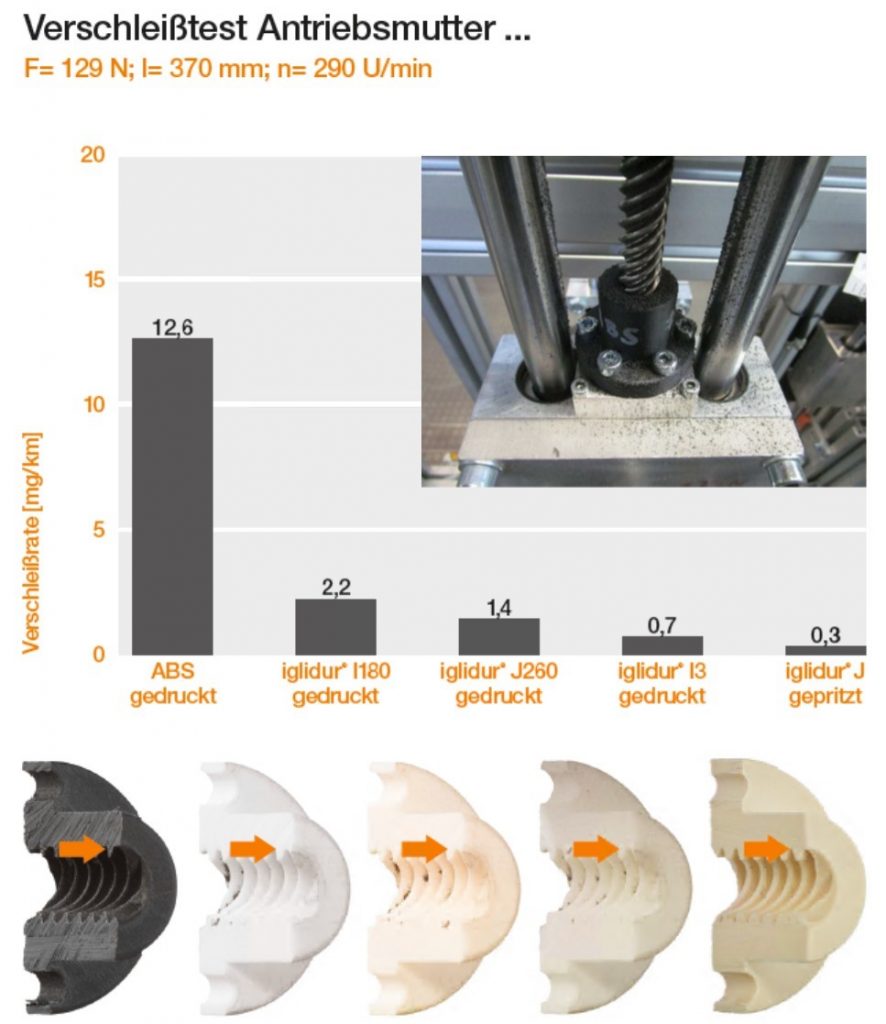
Sind Sie darüber hinaus auf der Suche nach der passenden Spindel zu Ihrer Antriebsmutter, können Sie diese in unserem Online Shop auch ohne tiefgehendes technisches Knowhow oder CAD-Software samt zugehöriger Zeichnung passend konfigurieren.