Which energy supply system makes sense for top drive systems?
Tim Schneebeck | 17. July 2020
The oil and gas business is not an easy one, especially in the so-called upstream production and extraction sector. Driven by the oil price, plants today have to work more and more efficiently to survive in the market.
Many of the plants currently in operation are either not automated or only semi-automated. The efficiency of these plants depends on the personnel and the low running costs. On the other hand, however, automation, as we know it from the automotive sector, is also making inroads into the oil and gas market. New plant comes onto the market that can be operated completely automatically – the rigs of the future! These systems have a much more complex structure and are more expensive to purchase. But they also work much faster and safer than their semi-automated sisters. So time is the efficiency criterion here.

The energy supply system at the centrepiece of the plant, the top drive, plays a decisive role in its efficiency. For older systems, the energy supply system must be as easy to maintain as possible and be cost-efficient. For new systems, the energy supply system must correspond to the degree of automation of the system, based on the time factor. igus has the right energy supply system for both system types.
The right energy carrier for semi-automatic oil drilling rigs – the e-loop!
For a classic oil drilling rig, an energy supply system that is easy to integrate and keeps the running (maintenance) costs low – this is where the e-loop comes in. This is characterised by the following points:
- Easy integration into (existing) plant
- Easy handling for the rig move process
- High cable protection through e-loop’s outer body (bumper) and high tensile force through plastic fibre rope in the centre of the e-loop.
- Modularity of the complete system which allows a quick and easy exchange of all single components (e.g. also single cables)
- Offers operational reliability due to secondary locking tension of all bolted connections
- Small bend radius of 500mm to minimise collisions and entanglements
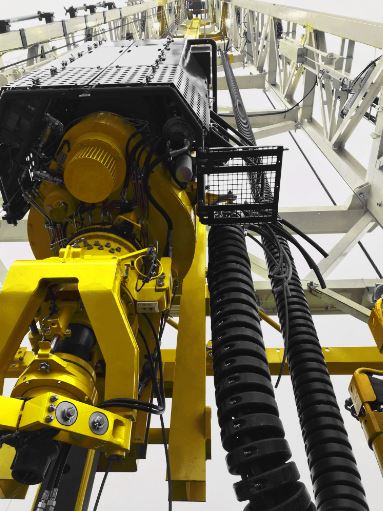
The e-loop is also the right choice for systems already running. A retrofit can minimise maintenance and servicing costs. Due to the high modularity it is possible to exchange all components like the e-loop outer body (bumpers) but also individual cables. This reduces costs and above all saves time in maintenance and servicing. It therefore increases the effectiveness of the system.
Further information about the e-loop: www.igus.eu/e-loop
The right energy supply system for (highly) automated drilling rigs – the e-chain!
For (highly) automated systems, I always recommend a chain solution as energy supply at the top drive or the pipe handler. Especially in the case of new buildings, these systems can be easily integrated. The approach here should be to design the energy chain with a trough guide. This makes it possible to keep the top drive with electric chain in the mast even during rig moves. It is even possible to replace plug-in connectors with a terminal box. This saves investment costs, but above all time, and thereby increases the efficiency of the plant. In addition, a correctly designed system requires almost no maintenance. Therefore, the right cables, which must be designed for continuous movement in the e-chain, are particularly important.
Further information about cables for continuous movement: https://www.igus.eu/info/unharnessed-cables-information-overview?L=en
If the motor cables (often multi-core) are divided into single cores, additional costs but also the bend radius of the system can be significantly minimised.
- A well-defined working area (“foot print”) of the e-chain within the system prevents collision with other equipment
- Integration of a guide trough can be carried out without problems in new buildings
- Structured interior separation of the cables increases the service life
- The top drive and trough system can remain in the plant during the rig move
- Plug-in connectors can be omitted when using a terminal box
- Bend radius of the e-chain can be significantly reduced by dividing the power cable into individual cores.
So you can see that the integration of an energy chain into the system involves more effort than with e-loop. This can, however, significantly reduce the effort required during installation and dismantling of the systems.
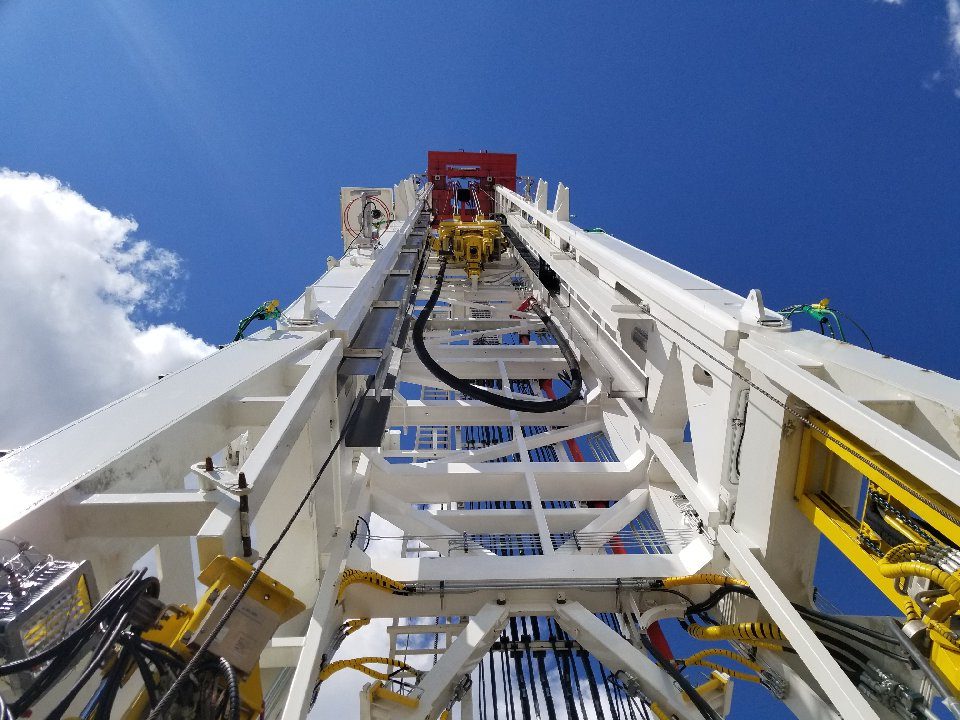
Further information about energy chains for top drive systems: https://www.igus.eu/info/industries-application-top-drive-system?L=en
Summarise the situations where a particular energy supply system makes sense
To sum up, it may be said that both energy supply systems, the e-loop and the energy chain, have their own individual strengths. It therefore makes sense to weigh up the advantages and disadvantages for each type of system. The e-loop shows its strengths primarily in conventional and systems already running (with service loops). Here it can score points due to reduced maintenance costs. The energy chain makes more sense for new buildings and highly automated plants. It impresses above all through shortened installation and dismantling times of the plants. Whatever type of system you have, we will be happy to help you make the right choice and also provide support for integration into your system.
Did you also know that we now also offer our energy supply systems for top drive systems with appropriate plug-in connectors as a plug & play solution? Have a look at our website: https://www.igus.eu/info/n20-heavy-duty-harnessing?L=en.