Roller energy chain as alternative to cable garland/cable trolley system
Theo Diehl | 1. April 2020
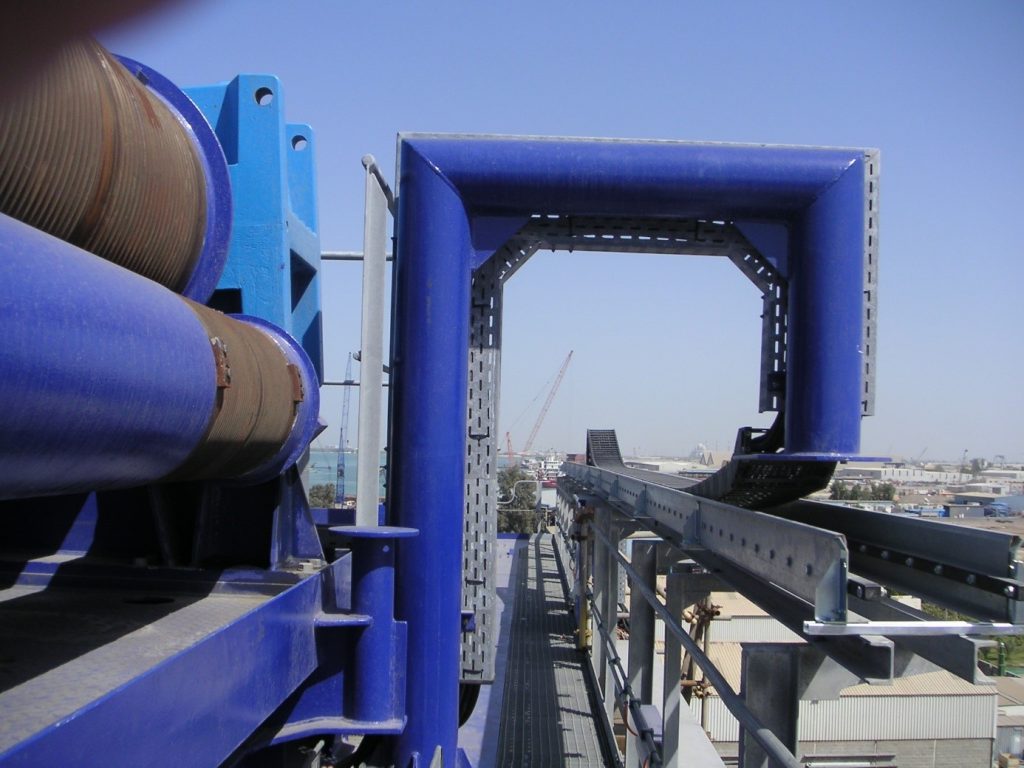
The advantages of the roller chain over conventional cable garland/cable trolley systems are obvious. Let’s take a closer look at the design features of both solutions – using harbour crane systems as an example.
System differences
In a festooning system, the cables are attached at the end of the travel and the cable loops are pulled all the way by the trolley.
In the energy chain solution, the cables are fed into the e-chain in the middle of the travel. The e-chain is pushed or pulled to halfway.
The cable feed in the middle of the travel saves more than 50% of the moving cables. This in turn results in a lower system weight on the crane and the current carrying capacity of the power cables is improved.
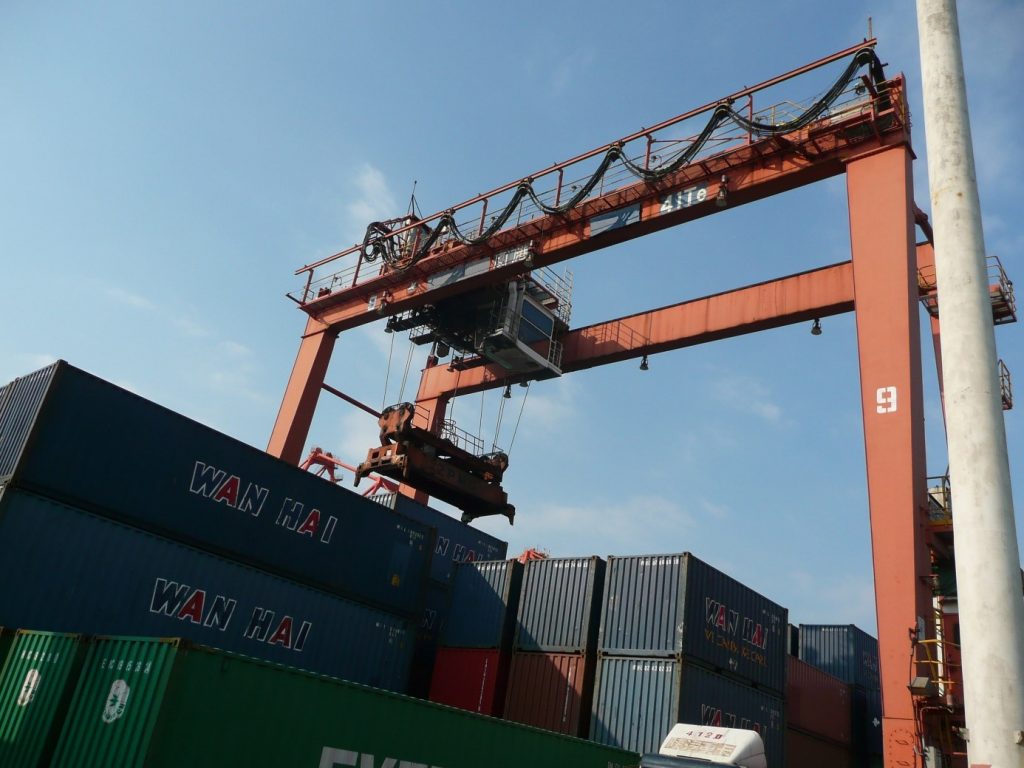
Influencing the crane girder structure
The energy chain system has a positive effect on the crane girder structure, since no steel construction/no additional weight is required for a cable station – which is necessary for cable trolley systems. Furthermore, the space for such a cable station is saved.
Dynamic parameters
Looking at the performance data of the systems in terms of speed and acceleration, a clear picture also emerges.
Cable trolley systems reach their limits at speeds of 240m/min and accelerations of more than 0.8m/sec2 . Whereas rolling energy chains can be operated at a speed of over 600m/min and with over 2m/sec2 acceleration.
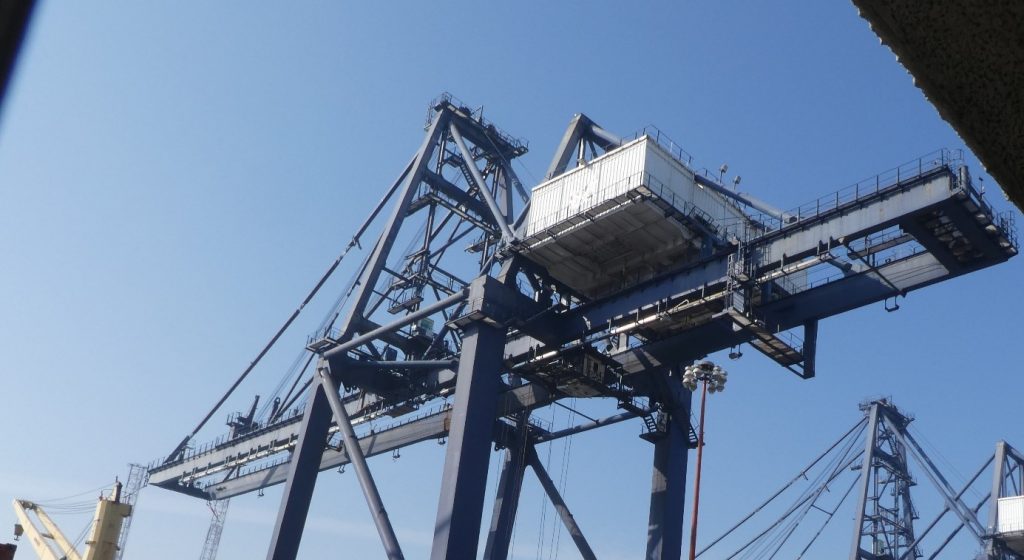
Benefits for the user
There are further advantages of the chain solution for the crane user. The main focus here is on safe plant availability.
In an energy chain system, all cables are protected by the e-chain in wind and weather. An unintentional cable movement or banging, as occurs with unprotected cable guidance in the festooning, is avoided. An attachment of the cables to the steel structure – e.g. during lateral acceleration on an ASC crane – is impossible with the e-chain solution.
The protection of the cables in the energy chain has a positive effect on plant availability. Unexpected downtime is avoided. The maintenance effort is minimised. Spare parts costs are reduced.
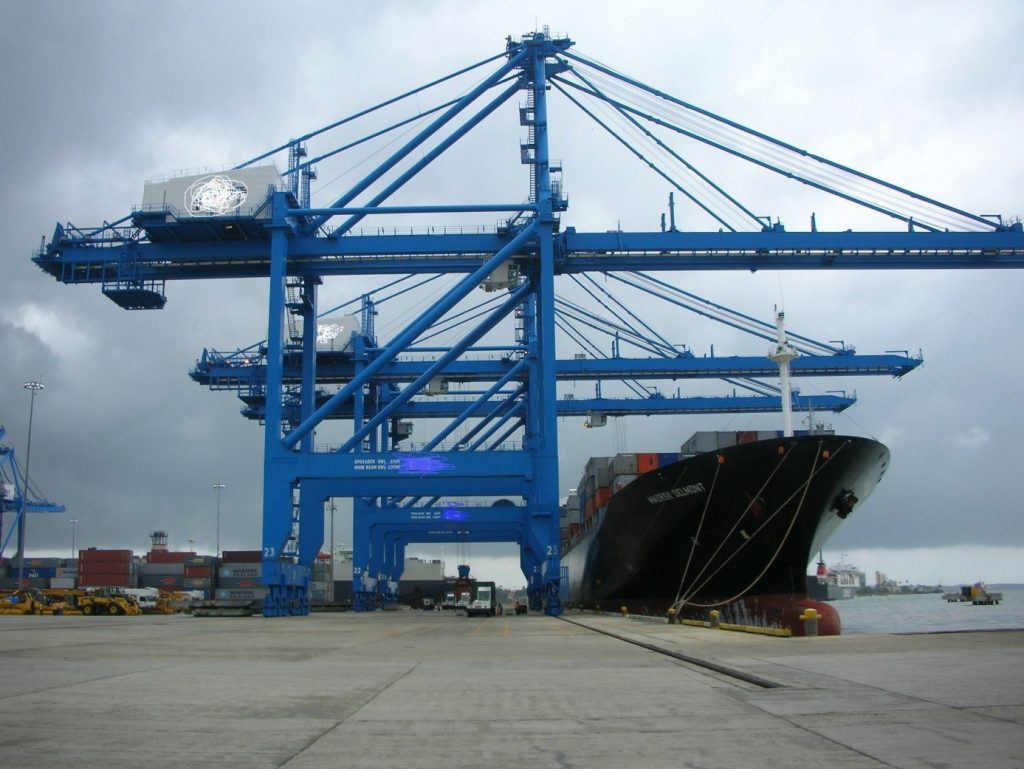
On our website, you will find more examples and solutions for cable guidance in harbour crane applications and our brochure that can be downloaded free of charge.
Do you have questions or an application that you would like to discuss with us? Arrange an appointment for virtual consultation now